Automotive Predictive Maintenance [IIoT CAN Data Loggers]
Need to get started with vehicle predictive maintenance?
In this practical intro you'll learn the top 4 benefits of IIoT predictive maintenance - and how to get started step-by-step. We also provide concrete use case examples.
Note: This intro focuses CAN bus assets (cars, trucks, machinery) - and how CAN bus data can be recorded and used in e.g. predictive maintenance dashboards.
If you're new to predictive maintenance, consider below simple definition:
The goal of predictive maintenance is to forecast and prevent equipment failure.
To make it slightly more concrete, we can put it into context:
Reactive maintenance: "If it's not broken, don't fix it". Best for cases where equipment failure is rare, easy to fix and with limited impact - e.g. switching a lightbulb in a warehouse.
Preventive maintenance: Also known as planned maintenance, this uses routine maintenance to diagnose equipment for failure. It works and is widely employed - but it is costly and does not capture asset-specific conditions.
Predictive maintenance: This involves collecting data from assets and using it to predict failure. This way, repairs can be done when needed (and avoided when not). It offers the best upside, but at the cost of complexity.
Equipment may include vehicles (trucks, cars, cranes, ships, tractors, ...) or machinery (robotics, conveyor belts, ...). As such, many target assets for predictive maintenance are based on CAN bus protocols (CANopen, J1939, OBD2, NMEA 2000, DeviceNet).
Further, predictive maintenance can be split into tiers (1.0-4.0).
At the basic level, predictive maintenance has been around for ages: When a technician inspects an asset and makes a change to avoid future failure, it is predictive maintenance.
The key change with '4.0' is the amount of data used, the update frequency and prediction models. Today, predictive maintenance 4.0 is achieved via IoT, big data and cloud analytics. This is also the type of predictive maintenance we will focus on in this article.
Top 4 benefits of IIoT predictive maintenance
Predictive maintenance is increasingly implemented in vehicles & machines - below we list the top benefits.
Reduced asset downtime
By predicting and preventing breakdowns, safety is improved and asset downtime can be reduced by up to 70% - boosting delivery accuracy and reducing costs
Extend remaining useful life
The life of assets like EV batteries and vehicle tires can be extended by using predictive models of e.g. SoC% to optimize charging & maintenance
Maintenance & parts optimization
Maintenance can be reduced by up to 50% via precision-scheduling of reviews/repairs, while inventories can be trimmed via 'remaining useful life' analysis of parts
OEM services & remote diagnostics
OEMs can offer predictive maintenance as a value-add service and e.g. reduce costs as technicians can analyze historical data & troubleshoot issues remotely
Which benefits are relevant to your IIoT predictive maintenance use case? Reach out for free sparring!
Contact usWhy use the CANedge CAN logger?
The CANedge CAN bus data logger offers optional GPS/IMU, WiFi and/or 3G/4G - ideal for predictive maintenance:
Log data out-the-box. Standalone. Link your vehicle to your server in <2 minutes
Extractable 8-32 GB SD. 2xCAN/LIN. CAN FD. Zero data loss. 50 μs RTC. Error frames. MF4
Only 8 x 5 x 2 CM. 100G. Robust alu enclosure. 5+ LEDs. Configurable 5V power out (CH2)
Built-in GPS/IMU. 3x accuracy via sensor fusion. Position, speed, distance & more
With the CANedge, predictive maintenance typically involves below steps:
#1 Setup your server: Set up your local/dedicated/cloud server via our guide in <5 min
#2 Configure: Configure your device with your server and WiFi or SIM details - and e.g. filters, triggers or transmit lists
#3 Record: Connect the device in your vehicle/machine to log raw CAN data
#4 Transfer: The device connects to your WiFi access point (CANedge2) or via 3G/4G (CANedge3) to auto-push log files to your server
#5 Process: Use the free Python API to DBC decode your data and set up your prediction model/logic - e.g. analyzing parameters vs. historical patterns
#6 Visualize: Finally, you can also visualize your data and set alerts via free, customizable browser dashboards. These alerts can serve as a simple predictive maintenance solution
The 'process' step is often further split into two steps for predictive maintenance:
- Predict: This involves using incoming data to predict the future, e.g. using linear regression models or simple thresholds. For example, if a specific parameter crosses a certain threshold, it may be considered 'predictive' of a potential future issue
- React: Once an issue has been predicted, the script should react - e.g. by sending a warning/notification by SMS, e-mail, slack, dashboard or similar to the relevant persons. A reaction can also be to e.g. auto-schedule maintenance or order spare parts.
Within CAN bus data logging, diagnostic trouble codes (DTC) are important indicators of issues within a vehicle. It is possible to request and record diagnostic codes across cars (OBD2 telematics), trucks (J1939 telematics), ships (marine telematics) and most other CAN use cases. The DTC information is recorded by the CANedge together with other raw CAN data and can be decoded via DBC files to human-readable form (e.g. an OBD2 DBC for cars or a J1939 DBC for heavy-duty vehicles).
You can use the DTC info for predictive maintenance in multiple ways:
- Alert: You can trigger alerts in your Grafana dashboard based on DTCs to send notifications
- Troubleshoot: DTC alerts can be visualized in your dashboard, letting you quickly diagnose issues by reviewing related data
- Automate: You can also use DTCs in scripts to e.g. trigger events (e.g. e-mailing data or scheduling maintenance)
- Train: The DTC information can be used to label 'issue states' in your data at scale for training predictive AI algorithms
Simple/advanced use of diagnostic trouble codes
Note that the use of diagnostic trouble codes in your predictive maintenance model will probably differ based on the issue you're trying to predict and your sophistication level.
For simple use cases, it may suffice to monitor the DTC information in near real-time and reacting swiftly upon them. In such a case, your predictive maintenance model is basically outsourced to the vehicle's existing diagnostic solution.
For more advanced applications, you'll probably instead aim to predict the issues that would trigger a DTC - before the DTC is actually triggered. Here, collecting raw CAN bus data signals (speed, temperatures, SoC, pressure variables etc) together with DTC information over longer periods can help in determining correlation patterns.
Software example: Set up browser dashboards & alerts
With the CANedge, you can easily set up free, custom browser dashboards for visualizing your data - and setting alerts.
check out the online playground - or learn more in our intro!
playground dashboards introPredictive maintenance use case examples
Below we provide practical examples of how the CANedge can be used for predictive maintenance.
Real-time monitoring of on-road vehicles
Need to avoid breakdowns for on-road vehicle fleets?
The CANedge3 can upload your CAN/LIN data (plus the internal GPS/IMU data) via 3G/4G using your own SIM card. This enables near real-time data transfer from e.g. automotives to a cloud server. On the server, data can be processed via Python scripts and visualized via predictive maintenance dashboards. If critical data limits are exceeded, your scripts or dashboards can send automated texts, e-mails or slack notifications. This enables simple vehicle predictive maintenance as part of your fleet management solution.
OEM predictive maintenance for machinery
Need to offer predictive maintenance & remote troubleshooting services?
As an OEM, you may offer predictive maintenance services as a product add-on. Here, the CANedge2 can be connected to equipment and upload operational data via the client's WiFi. The OEM can use the data to predict breakdowns, provide KPI reports, strategic sales etc. If issues arise, the OEM can access asset data via e.g. CANcloud and perform remote diagnostics. Further, via over-the-air updates, the OEM can reset a faulty machine remotely by making the CANedge2 transmit specific CAN messages.
Case study: J1939 predictive maintenance
Learn how one of our larger OEM customers use the CANedge2 to collect CAN bus data from heavy machinery in the field - and use it to perform simple automated predictive maintenance.
"Both the hardware and support from CSS Electronics have been outstanding!"
full case studyFAQ
Predictive maintenance is a rapidlly growing trend. The rise of Big Data, IoT, Cloud and AI is driving predictive maintenance with a 40% CAGR towards $10+ bn by 2022.
The growing focus is also seen in Google Trends, showing a 400%+ increase in interest since 2008.
Despite the growing interest, implementation remains a challenge. In a 2017 survey of 280 companies PwC found that only 11% have reached 'predictive maintenance 4.0' maturity (i.e. using big data to do predictive analytics) - though 47% plan to implement it in the future. We believe part of this disconnect is due to the lack of simple solutions to get started - which is what we address in this article.
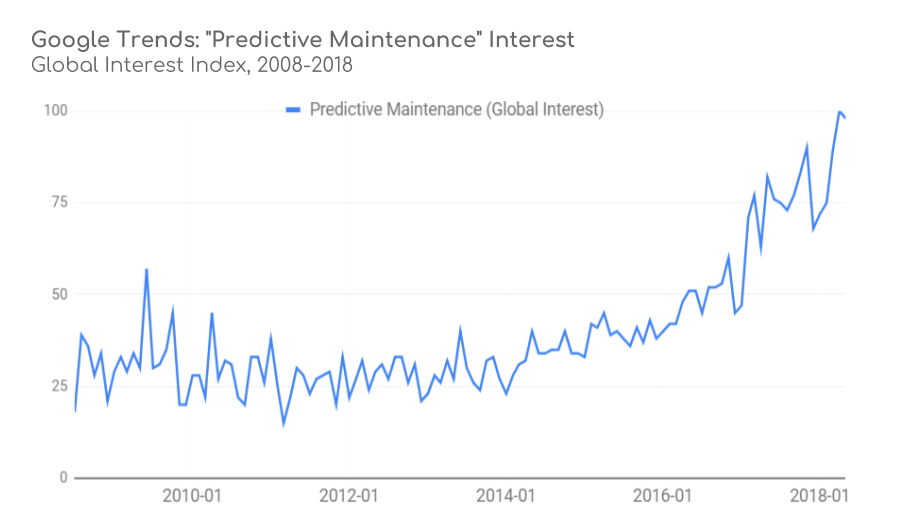
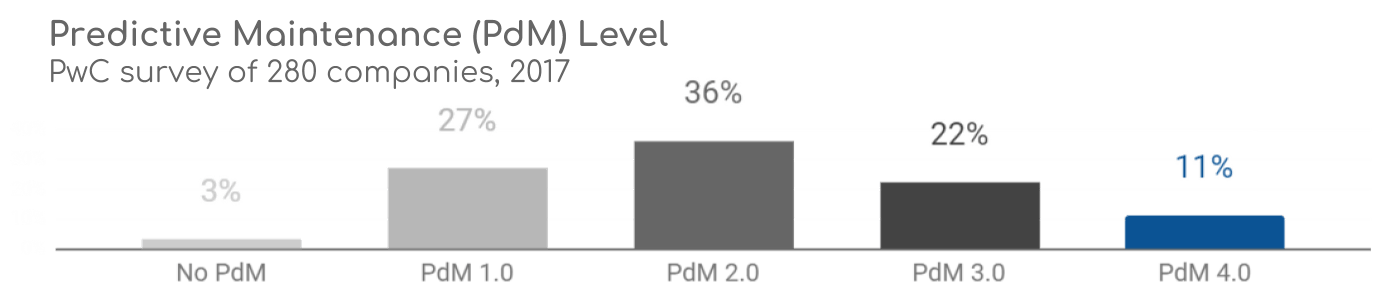
To make the 'prediction' in predictive maintenance more clear, consider the below practical examples:
Example #1 - The Oil-Sensitive Truck: In this Google Sheets illustrative example we consider a vehicle where the only possible failure is from not refilling the oil. Over time, the oil level decreases to 10% and the vehicle breaks down - i.e. the 'Remaining Useful Life' (RUL) is zero. For simplicity, we pretend that we observe the true RUL and adapt a simple linear regression. With this we predict the RUL out-of-sample and decide a time for warning - which in the example is ~17% off vs. the true RUL. You can copy and try the example yourself.
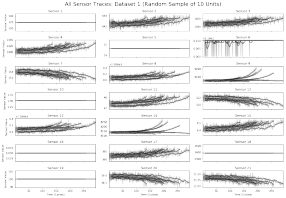
Example #2 - NASA Turbofan Engine: We strongly recommend reading this practical intro by Ben Everson. In short, he takes outset in NASA's 2008 Turbofan Engine Degradation simulation data set), which contains training & test data on 10 engines equipped with 20+ sensors. The goal is similar to Example #1, but in a more realistic context. In particular, this is helpful if you're about to get started with the basic data cleaning & statistical considerations. Check out both his intro and follow-up!
As established, predictive mainteinance can yield massive benefits - in particular within vehicle fleet management. Despite this, few fleet managers have implemented any form of predictive maintenance for a number of reasons:
- Lack of CAN data: Most vehicle fleet telematics solutions only monitor GPS data with limited predictive applications
- Proprietary CAN data: While a lot of data is often accessible via OBD2/UDS/J1939/FMS, critical data may be proprietary
- No requests: DTCs are often key to predictive maintenance, but most telematics devices do not enable request of these
- Reactive data usage: Some vehicle fleets do record FMS/J1939 data, but only use it reactively (e.g. to track fuel usage)
- System lock-in: The under-utilization of data is often linked to vendor lock-in and restrictive outdated telematics platforms
The CANedge2 is ideal for fleet management solutions where access to CAN data is required. It lets you record all the raw CAN data and auto-push it to your own server. Here, you'll be able to decode the data via DBC files, which makes it flexible in case you e.g. later need to added additional parameter decoding rules (for example from reverse engineering efforts).
Further, the CANedge software/API tools are 100% free and designed for interoperability. This means your team can start small and gradually increase the sophistication level of your predictive maintenance solution - while ensuring zero vendor lock-in.
To learn more about using the CANedge2 for predictive maintenance fleet management, contact us.
The 'prediction' examples illustrate that adding more data quickly adds complexity. For this reason, using machine learning (ML) has become popular in predictive maintenance models.
Machine learning is a natural fit as predictive maintenance involves failure classification using huge amounts of sensor data. We won't dive deeper into this here, but consider reading this InfoQ technical intro or this Azure AI article using the NASA Turbofan data with ML.
Further, if you're interested in a bit more detail on the predictive models for PdM, check out this article by BigData Republic - it's a great read, in particular to provide context for the RUL modelling strategy in the 'prediction' examples above.
-
Changing your culture - predictive maintenance is unknown territory to most corporate leaders. To succeed, you'll need a clear sponsor and to start with a simpe proof-of-concept
-
Choosing the right IoT solution - the market for IoT devices is complex. The CANedge2 may be the right fit for you, but we recommend reaching out to get sparring on your use case
-
Managing big data - processing big data can be difficult. Set the right team and begin with few parameters. But: Historical data is vital, hence it is vital to get started
-
Avoiding data lock-in - most IoT solutions lock your data in the their cloud. However, this data and the capabilities learned may become your top differentiators. Own your solution
-
Building your model - your prediction methodology & model should match your capabilities. Don't choose a big outsourced model you don't understand if it's not a fit. Start simple
We see these challenges in action regularly - contact us for input on how to solve them.
The key to begin your predictive maintenance journey is to start small. Below we provide 9 steps to get started:
- Identify a pain point: select an asset that is known to break down regularly and is based on CAN bus
- Set a team : Dedicate 1-3 persons to implement the PoC, including one with expertise on interfacing with the asset
- Define a prediction model: Identify which failure you'll predict and set up a basic model (e.g. based on parameter thresholds)
- Source IoT device: Get 1-2 CANedge2 units to test the basics (logging raw data, decoding it via a DBC, setting up WiFi/server)
- Start collecting: Install the CANedge2 and establish a basic data collection flow to your server
- Train the model: Based on incoming data (incl failure data), "train" your model (e.g. adjusting parameter thresholds manually)
- Predict 1st breakdown: With your basic model in place, the next step is to actually predict a breakdown before it happens
- Add reaction: Set up a basic reaction flow - e.g. set your script to trigger an email if an issue is predicted
- "Sell" solution: Present the proof of concept & results internally to get the buy-in and funding to scale-up
Yes - we work with several end users that deploy various forms of predictive maintenance in practice. As such, we're happy to provide free sparring on your specific use case. Just contact us to set up an initial conference call.
Ready to start your predictive maintenance pilot?
Get your CANedge2 today!